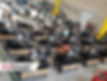
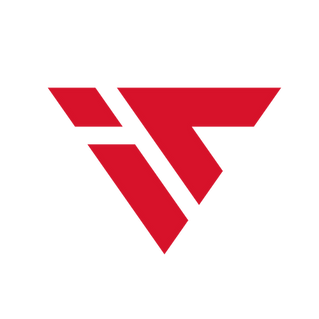_edited_edited.png)
How
we work
Our method, our passion.
01
It is at this stage that the design philosophy of Italtower staff emerges.
Mechanical design is the first stage in the construction of a lighting tower.
Design
02
The production phase includes cutting the carpentry and poles, painting and assembling these components with the generator we have developed.
Production
03
Check
The Final Check involves a series of activities necessary to establish the suitability of the product before placing it on the market. Test procedure that allows 100% functioning to be tested.
Support after the sale is one of the most important phases that Italtower wants to provide. Dedicated customer support for warranties and spare parts.
04
Support
01
Product design

Design
It is at this stage that the Italtower staff's design philosophy emerges, seeking simple solutions to realize innovative and functional ideas. Together we define shapes inspired by what we have around us: (octagons), colours, surface finishes and all details, with all possible design variables including customer requests, whether aesthetic, ergonomic or functional.
Engineering
Mechanical design is the first stage in the construction of a light tower with drawings of assembly and parts assemblies and bills of materials. Italtower's technical staff carefully manage each project phase, which is fundamental for the optimization and control of schedules and, above all, costs.


Prototypes
Prototyping is an important step that is done before industrialising the product, as it allows for dimensional, functional and stability verification. We produce a functional prototype that highlights all the important points of the machine:
-
We verify any design problems that did not emerge in the 3D design phase.
-
We carry out all market testing, research and verification, perhaps by exhibiting them at events or giving them to our distributor partners for use and verification.
Feasibility analysis
The first phase to be tackled, perhaps the most important, is the Feasibility Analysis that can give substance to a project request. It is essential, therefore, to collect all the key points of the project in such a way that any critical points can emerge immediately so that they can be remedied before the start of planning. This is followed by a comprehensive study of materials, the choice of suppliers and a program of the production process.

02
In-house production
Laser cutting of sheet metal
(Machine structure)
After loading the defined three-dimensional design, the sheet metal is cut. In laser cutting, a beam of radiation is generated and focused through a lens onto the surface of the sheet metal to be cut, which heats up and quickly melts.
At the same time, a flow of gas from a nozzle downstream of the focusing lens produces a thrust strong enough to push the molten metal away, effectively generating the cutting groove. The process continues by moving the laser beam and the sheet metal along the desired cutting path.
The advantages of laser cutting are that it does not leave ragged edges but is able to make very clean cuts. Again with the laser, all types of holes are drilled with great precision, total absence of burrs and speed, and special shapes can be obtained with some ease.

Laser cutting
of poles
(Tower poles)
The use of laser technology in square tube cutting has enabled us to achieve significant advantages in innovation of the production process and a high level of quality.
By improving machining operations such as drilling, slotting, notching, allowing perfect fits without burrs and optimizing subsequent welding operations, we reduce machining times.
The 3D projects are loaded that allow you to use the files for the programming of the processes in a faster and more effective way.

Galvanizing
Galvanizing is the process by which a zinc coating is applied to a metal product generally made of steel to protect it from galvanic corrosion. Italtower carries out the galvanizing processes on all the moving parts of its lighting towers with the electrolytic galvanizing method. This type of processing is known as 'cold' galvanising.
The final result is an optimal product both on an aesthetic and functional level.
In electrolytic galvanizing, the material to be treated is adequately prepared in 3 main phases: the preparation of the surfaces to be treated, the coating and the finish.
All our components are pre-degreased, pickled and finally degreased, they are then immersed in an electrolytic solution containing zinc salts. Finally, the last passivation phase guarantees greater resistance to corrosion.
Painting
All Italtower products are treated with powder coating. This fundamental finishing step has two important purposes: on the one hand the aesthetic characterization of the products, on the other their functional improvement. The latter effect is due to the fact that the paint layer makes the metals more resistant to wear and tear and degeneration once in contact with the external environment, thus extending their duration over time.
The thermosetting powder coating guarantees excellent mechanical and aesthetic properties that make the treated objects resistant to atmospheric agents, guaranteeing their protection over time.
All the details undergo a complete treatment in these steps:
-
Phospho-degreasing tunnel
-
Drying oven at a temperature of 160 °C
-
First annual and second automatic powder painting booth
-
Electrostatic fixing of powders
-
Baking oven with automatic temperature control according to the curing temperature of the different powders and the thickness of the materials to be painted

Assembly
Every single phase of the assembly process is meticulously optimized, with a rigorous control of the logistical aspects of handling the components in line and in the warehouse. Some employees take care of the procurement of materials for the assembly and handling of the complete machines.
Workstations, assembly lines, handling are constantly monitored. We are therefore able to provide progressive improvements to the assembly level.
Organization of warehouse stocks and restocking, arrivals and shipments.
By means of management software, we ensure constant control of both inventories and commitments for production and started production lines. Based on both planned production and what we expect to need, we then place reorders according to delivery times. Each operator is trained on the importance of keeping data regularly updated in order not to have errors on stocks and inventories.
Work scheduling
Italtower is able to handle the constant variations in production plans. Each of our operators is interchangeable allowing the variability of the lighting tower to be assembled. The wide range and customizations required have made us highly flexible and available to market requests.
03
Final check

Testing
Italtower has adopted a comprehensive testing procedure that allows for 100% testing of the lighting tower's performance.
Italtower's technical staff carry out the following tests and checks on all machines:
-
Functional efficiency test.
-
Proof of effectiveness.
-
Safety test.
These checks are used to verify the operation and performance of the light tower, whether it is purely electrical or equipped with an internal generator, to ensure optimum quality.
During the testing of the model with internal generator, the lighting tower is subjected to an electrical load to simulate operation in the heaviest condition of the generator.
Shipment
Italtower personally oversees every step of this process: a competent and professional team will help you decide on the best shipping option, with constant monitoring of the goods right up to their final destination.
Product packaging is a key aspect to which Italtower pays great attention. Transported by road or container, your light towers will arrive at their destination safely and in the shortest possible time.

Spare parts
Our spare parts are always available in our warehouse.
Possibility of organizing any shipments of components to our dealers in 24 hours thanks to a widespread and efficient logistics network
The advantages:
-
Certified reliability of the range of original components, fully managed by Italtower and with the collaboration of our selected partners and suppliers.
-
Controlled processes thanks to strict production standards.
-
Lower total cost of ownership and higher residual value in stock.
-
Assistance and experience thanks to a technical staff that knows the products down to the smallest detail.

Warranty
Italtower offers a minimum guarantee of 1 year on each product, which can be extended up to 24 months in total. After a brief report of the component malfunction, Italtower will replace it quickly. Our assistance services are constantly available to our customers.
Italtower has an international distribution network with well-trained companies capable of providing an excellent service to the end customer.