
_edited_edited.png)
How
we work
Our method, our passion.
01
It is at this stage that the design philosophy of Italtower Staff emerges.
.
Mechanical design is the first stage in the construction of a light tower.
Design
02
The production phase includes the cutting of carpentry and poles, painting and the assembly of these components with the generator we developed.
Production
03
Check
The Final Check involves a series of activities necessary to establish the suitability of the product before putting it on the market. A test procedure that allows for 100% testing of operation.
.
04
Support
The support after the sale is one of the most important phases that Italtower wants to provide. Dedicated technical assistance to the customer for warranties and spare parts.
.
01
Product design

Design
It is at this stage that the Italtower staff's design philosophy emerges, seeking simple solutions to realize innovative and functional ideas. Together we define shapes inspired by what we have around us: (octagons), colours, surface finishes and all details, with all possible design variables including customer requests, whether aesthetic, ergonomic or functional.
Engineering
Mechanical design is the first stage in the construction of a light tower with drawings of assembly and parts assemblies and bills of materials. Italtower's technical staff carefully manage each project phase, which is fundamental for the optimization and control of schedules and, above all, costs.


Prototypes
The creation of prototypes is an important stage that is done before industrialising the product, as it allows us to carry out dimensional, functional and stability checks. We produce a functional prototype that highlights all the important points of the machine:
-
We check any design problems that did not emerge in the 3D drawing phase.
-
We carry out all market testing, research and verification, perhaps exhibiting them at events or giving them to our distributor partners for use and verification.
Feasibility analysis
The first and perhaps most important phase to be tackled is the Feasibility Analysis, which can give substance to a project request.
.
it is essential, therefore, to collect all the key points of the project so that any criticalities can emerge immediately in order to remedy them before the start of the project. This will be followed by a complete study of materials, the choice of suppliers and a programme of the production process.
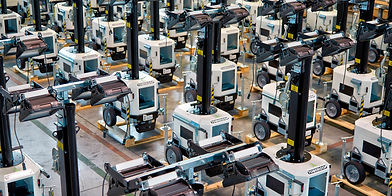
02
In-house production
Sheet metal laser cutting
(Machine structure)
.
After loading the defined three-dimensional project, we proceed with the cutting of the sheet metal. In the laser cut a radiation beam is generated, focused through a lens on the surface of the sheet metal to be cut, which heats up and quickly melts.
A stream of gas exiting from a nozzle downstream of the focusing lens produces a thrust sufficiently intense to push the molten metal away, effectively generating the cutting groove. Processing proceeds by moving the laser beam and the sheet metal along the desired cutting path.
.
I advantages of laser cutting are that it does not leave any rough edges but is able to make very clean cuts. Also with the laser, all types of holes are made with great precision, total absence of burrs and speed; furthermore, particular shapes with some ease.

Laser cutting
of poles
(Pole tower)
The use of laser technology in square tube cutting has enabled us to achieve significant advantages in innovation of the production process and a HIGH level of quality.
By improving machining operations such as drilling, slotting, notching, allowing perfect fits without burrs and optimising subsequent welding operations, we reduce machining times.
3D projects are loaded, allowing files to be used for programming machining operations more quickly and efficiently.

Galvanizing
Galvanising is the process by which a coating of zinc is applied to a metal artefact, usually steel, to protect it from galvanic corrosion. Italtower carries out galvanising processes on all the moving parts of its light towers using the electrolytic galvanising method.
This type of processing is known as cold galvanising. The end result is a product that is both aesthetically and functionally optimal.
In electrolytic galvanising the material to be treated is adequately prepared in 3 main phases: preparation of the surfaces to be treated, coating and finishing.
All our components are pre-degreased, pickled and finally degreased, then immersed in an electrolytic solution containing zinc salts. Finally, the final passivation phase ensures greater corrosion resistance.
.
Painting
All Italtower products are treated with powder coating. This fundamental finishing step has two important purposes: on the one hand the aesthetic characterisation of the products, on the other their functional improvement. The latter effect is due to the fact that the layer of paint makes the metals more resistant to wear and tear and degeneration once in contact with the outside environment, thus prolonging their service life.Thermosetting powder coating guarantees excellent mechanical and aesthetic properties that make the treated objects resistant to atmospheric agents, guaranteeing their protection over time.
All parts undergo complete treatment in these steps:
-
Phospho-degreasing tunnel
-
Drying oven at a temperature of 160°
-
First annual and second automatic powder coating booth
-
Electrostatic Powder Coating
-
Baking oven with automatic temperature control according to the curing temperature of the different powders and the thickness of the materials to be coated

Assembly
Every single step of the assembly process is meticulously optimised, with strict control of the logistical aspects of component handling on the line and in the warehouse. Workers take care of the procurement of materials for assembly and the handling of complete machines.
The workstations, lines and lines are designed to meet the needs of the customer.Workstations, assembly lines, and handling are constantly monitored. We are therefore able to provide progressive improvements in the assembly level.
.
Organisation of warehouse inventories and replenishment, arrivals and shipments.
By means of management software, we ensure the constant control of both warehouse stocks and commitments for production and in the production lines started. On the basis of both planned production and what we expect to need, we make reorders according to delivery times. Each operator is trained on the importance of keeping data regularly updated in order not to have errors on stock and inventories.
.
Programmazione del lavoro
ITALTOWER is able to manage the constant changes in production plans. Each of our operators is interchangeable, allowing the variability of the light tower to be assembled. The wide range and customisations required have made us highly flexible and available to market demands.
03
Final check

Testing
ITALTOWER has adopted a comprehensive testing procedure that allows for 100% testing of the light tower's performance.
Altower's technical staff performs the following tests and checks on all machines:
-
Functional efficiency test.
-
Efficacy test.
-
Security check.
These checks are used to ascertain the operation and performance of the light tower, whether it is purely electrical or equipped with an internal generator, to ensure its optimum quality.
During testing of the Model with internal generator, the light tower is subjected to an electrical load to simulate operation under the most severe generator conditions.
Shipment
ITALTOWER takes care of every step of this process: a competent and professional team will help you decide on the best shipping option, with constant monitoring of the goods right up to their final destination.
Product packaging is a fundamental aspect to which Italtower pays great attention. Whether transported by trailer or container, your light towers will arrive at their destination safely and in the shortest possible time.

Spare part
Our spare parts are always available in our warehouse.
Able to organise any parts shipments to our dealers within 24 hours thanks to our extensive and efficient logistics network.
The advantages:
-
Certified reliability of the original parts range, totally managed by Italtower and with the collaboration of our selected partners and suppliers.
-
Controlled processes thanks to strict production standards.
-
Lower total cost of ownership and higher residual stock value.
-
Support and experience thanks to a technical staff that knows the products down to the smallest detail.
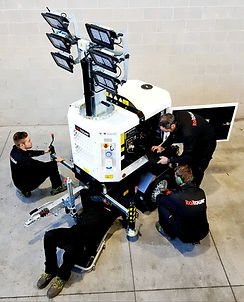
Warranty
ITALTOWER offers a minimum 1-year warranty on each product, which can be extended up to 24 months in total. After a brief report of the component malfunction, ITALTOWER will replace the component within a short time. Our support services are constantly available to our customers.
.
ITALTOWER has an international distribution network with trained companies able to provide excellent service to the end customer.